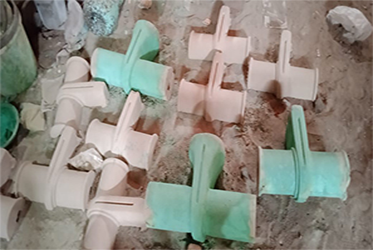
Any component of a casting that cannot be sculpted by the major removable pattern is given shape using a core, which can be either a sand or metal insert. A concave impression is left in sand when a design is pushed into it and subsequently removed. This gap is filled by liquid metal when it cools. To enable more design complexity, cores are constructed. In a casting, well-built cores produce holes or chambers. Up to five cores may be present in automotive engine moulds to produce the chambers required for a combustion engine to function.Additionally, cores can be used to make angles that a pattern would not be able to produce. It would be impossible to remove the pattern without fracturing any overhangs above empty spaces. These situations allow for the employment of a core.Internal core castings typically contain a hole in the outer shell of the mould that can be used to remove the core after casting, though this hole may be mechanically closed off during finishing Casting in Ahmedabad.
Sand-based cores are created to disintegrate; towards the end of the casting process, internal cores are quite literally shaken out of the casting. The "shakeout" opening is useful for positioning the core as well. A core must "bridge" the space to be filled without touching any sides in order to get a constant thickness of metal since any area where the core hits the mould prevents molten metal from flowing there. In order to accomplish this, the core is typically longer than the casting and is secured in place by sand divots outside the casting pattern.